What are Appropriate Boiler Blowdown Design Parameters? – Designing recommendations for both continuous surface and intermittent bottom blowdown
June 19, 2019 by Aaron Rhoade
When designing a new boiler room or making changes to an existing one, one small but pertinent aspect of this is coming up with the appropriate blowdown design percentage for both surface blowdown and bottom blowdown. What is a good rule of thumb to be used as the minimum amount of blowdown to design around? How much is too much? This Madden Manufacturing article will walk through these providing guidance to the questions and explaining why you need to be blowing down your boiler(s) in the first place.
Let’s start with bottom blowdown, what is intermittent bottom blowdown, why is it used on every industrial boiler, and how much are you supposed to do?
Intermittent Bottom Boiler Blowdown
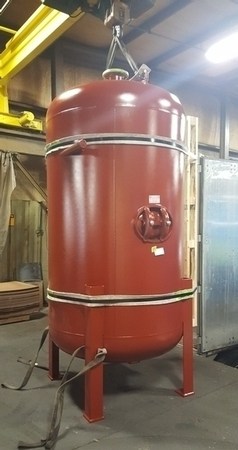
What is it? – Intermittent bottom blowdown is most often simply a manual valve that is opened wide on the bottom of the boiler. For industrial boilers, the blowdown line is often 1 to 2”.
Why is it used? – Blowing down water from the bottom of your boiler rids the system of settled impurities in the water. During the process of boiling, various impurities form and settle to the bottom. Sediment and other crud keeps the boiler from boiling as efficiently as possible. Any impurities in the boiler water can slow down heat transfer from the water tubes or fire tubes in the boiler thus causing you to burn more fuels than would otherwise be necessary.
So how much should we blow down? – The National Board Rules and Recommendations for the Design and Construction of Boiler Blowoff Systems states blowoff tanks, more often called blowdown tanks, should be sized with a holding capacity at least equal to the volume of water removed from the boiler when the normal boiler water level is reduced by 4 inches.
In simpler terms, as a general rule of thumb, most operators will open up the valve for 30 seconds to 1 minute to rid the boiler of settled, dirty water.
As alluded to in this section, special equipment is required for intermittent bottom blowdown. It is against EPA requirements to directly blowdown hot, dirty boiler water into a sewer due to possible hazards to life and/or property. This special equipment is often either a traditional overflow style blowdown tank, or a small, compact blowdown separator. You can learn more about these systems by reading our blog (link) or visiting our webpage (link).
Continuous Surface Boiler Blowdown
Continuous surface blowdown for boilers is often a bit more involved than designing equipment for intermittent blowdown. This is due to the process more or less being a constant 24/7 application which thus makes it economical to also try to recover heat from the blowdown on top of cooling it to a safe temperature. Let’s break it down.
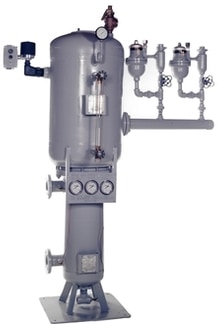
What is it? – Continuous surface blowdown is often a 1” port/blowdown line coming off the boiler at the normal water level. Nowadays, the most common way to do this is via TDS (total dissolved solids) system that continually measures conductivity in your boiler water and blows down a little more or a little less depending on the amount of conductivity to maintain a healthy level. As stated several times now, this is an ongoing, continuous process. Think slow and steady. Another way to achieve appropriate continuous blowdown is manually with a rugged metering valve like Madden’s orifice meter. These manual meters offer more durability and a longer service life than most TDS systems which often use needle type valves. You can read more on our boiler blowdown valves here (link).
Why is it used? – Continuous surface boiler blowdown is used for the same reasons intermittent bottom blowdown is used, ultimately to keep your boiler water clean to allow for efficient boiling as possible. On large enough industrial boilers, enough boiling can be occurring to produce suspended solids in the water. These impurities can cause scale build up on fire tubes and water tubes as well as cause a layer of scum on the surface of the water. Both of these imperfections in the process can act as an insulator to heat transfer. Which again, will cause you to burn more fuel than you would need to otherwise. Continuous surface blowdown saves you money on fuel costs. And on top of that, as mentioned earlier, you can recover heat from this blowdown.
There is a vast amount of recoverable BTU’s in surface blowdown water, they are recovered via flash steam and heat transfer. Madden Manufacturing makes complete boiler blowdown heat recovery systems which achieve both of these processes and our units often pay for themselves in 6 months or less. You can read more about them here (link).
So how much should we be blowing down? – In the case of continuous surface blowdown, there is not a National Board booklet to fall back on, but there are recommended levels of TDS to target. For these levels and/or a detailed recommendation/analysis you would want to reach out to the boiler manufacturer, a chemical engineer, or TDS system supplier.
This also relates to using manual boiler blowdown valves. Based on your targeted TDS levels we would help recommend an orifice meter that offered the appropriate range of blowdown flow control so that your blowdown percentage achieved efficient levels of solids. For a Madden boiler blowdown orifice meter, this is based on boiler operating pressure and orifice size in our orifice plates.
But whether you’re manually controlling your boiler’s surface blowdown or automatically controlling it, as a general rule of thumb, we would recommend your maximum design parameters fall somewhere between a blowdown rate of 5-10% of your steam production.
At Madden Manufacturing, if an end user or engineer approaches us for a boiler continuous blowdown heat recovery system, and they do not have a maximum design parameter our standard is to design a system to have a capacity of 5% of steam production if we are expecting clean R.O. water to be used; and we would jump this to 10% in cases where someone suggest they would eventually like to add boilers to the room, or if they know their boiler feed water will have a significant amount of impurities that can’t be removed before hand.
Most surface blowdown applications are going to hover around 3-5% blowdown when it comes to the normal, or average, blowdown rate. Any significant spikes above this are likely due to a special circumstance, again think slow and steady. So unless your boiler water is known to be extremely dirty, 5% is usually an appropriate maximum design parameter for most industrial boiler systems, with 10% being a “better safe than sorry” capacity.
If you have a case where you’re thinking the heat recovery system capacity should be above 10%, we would caution you to contact us to discuss your application further. The reason for this, usually the cost difference between units with capacity falling within the ranges we’ve discussed, 5-10%, is relatively minimal when you factor in everything there is to consider. The main thing to consider being how heat recovery systems pay for themselves via fuel cost savings. So spending a bit more for this “better safe than sorry” feeling can certainly be appropriate. BUT, once we start to consider a heat recovery system that is sized higher than 10%, we will begin to reach the point of the system becoming an uneconomically friendly investment. If you are worried your boiler will consistently need to blowdown more than 10% of its steam production then there is likely other issues you would want to look at.
For any general questions, concerns you may have with your blowdown design, or for a quote, please feel free to call us up to discuss these topics further.
Conclusion
Designing all of the necessary equipment for boiler blowdown water applications is often an afterthought in the boiler room as there are more essential things to consider first. But it is a very vital process to the boiler(s) nonetheless. Madden Manufacturing and our team of distributors would love to help make recommendations and/or design this equipment for you. We have been working with boiler blowdown equipment for over 65 years now and hope our knowledge and responsive service will be just what you’re needing.