What are the Differences between the Boiler Blowdown Heat Recovery System Design Options Available on the Market?
December 11, 2020 by Aaron Rhoade
If you are looking to specify or purchase a boiler blowdown heat recovery system you’ve likely noticed there are a handful of designs to choose from. This article will walk you through the different choices available on the market and describe the strengths of each.
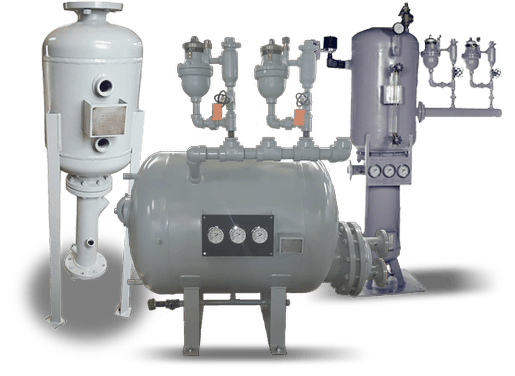
If interested in the general purpose and function of boiler blowdown heat recovery systems you can find them (here) where we have written several other articles covering these topics.
In summary, boiler blowdown heat recovery systems perform two essential tasks for continuous boiler surface (top) water blowdown. First, they provide a low pressure flash vessel to take the hot, high pressure saturated water blowing down from the boiler and safely separate steam and condensate. This steam is sent back to the deaerator tank. Second, they cool the remaining condensate with a heat exchanger of some type using the boiler’s makeup water as the cooling medium. Both of these processes put heat back into the system, the first via pure steam vented back into the D/A tank, the second via mechanically pre-heated makeup water.
This reclaimed heat is put back into the system using natural conduction, in other words, no fuel or electricity used. Since this is heat that would have otherwise been wasted to the drain, this process is therefore called “heat recovery”. These units often pay for themselves in less than a year by reclaiming this heat and lessening the fuel consumption requirements the boiler would otherwise call for.
Now, let’s take a look at your heat recovery system design options that provide these services. Most O.E.M. providers of this equipment use the same terms for their designs, either Continuous Blowdown Heat Recovery System or Boiler Waste Heat Recovery System. So for the purposes of this article we have separated the design differences with our own terms.
“Maintenance Friendly”, “High Capacity”, and “Most Compact” designs.
“Maintenance Friendly” Heat Recovery System Designs
What we are defining as maintenance friendly designs are the heat recovery systems that separate all the local components involved in the system. The heat exchangers are completely detached from the flash vessel, the level controls are all external, and everything is then plumbed together on a common skid. Most of the time these will come with a roughly 16” diameter and 56” height flash vessel and then a shell and u-tube style heat exchanger. Occasionally the heat exchanger would be a plate and frame type.
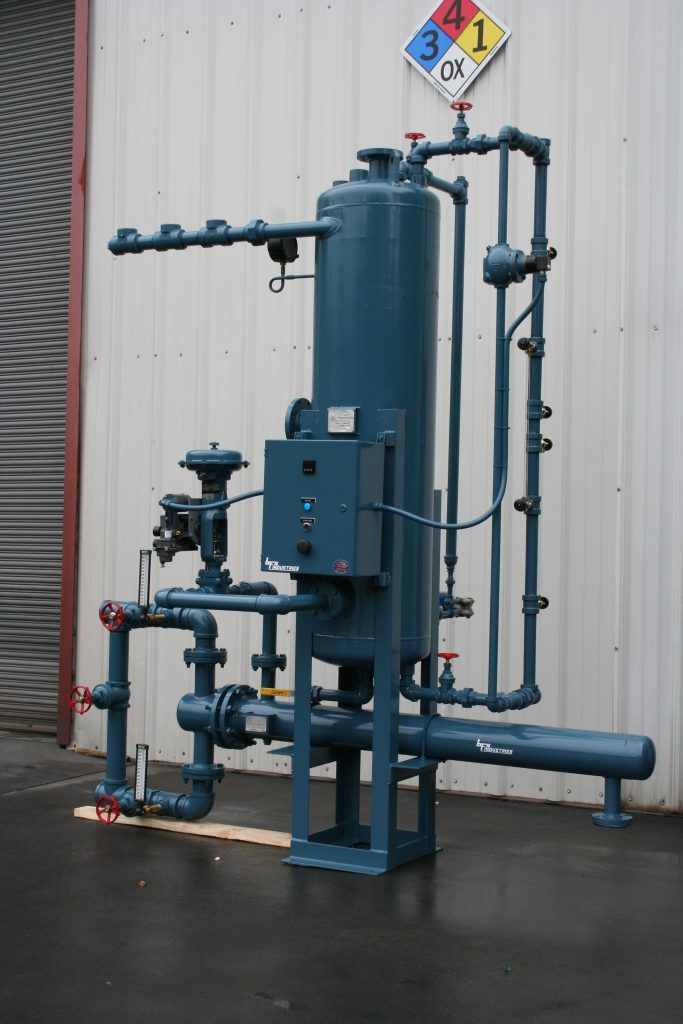
See picture of a BFS Industries unit for reference.
Pros:
- All components can be isolated for maintenance.
- Shell and u-tube style heat exchangers are very efficient.
- Ancillary equipment options are easily changed out to your preference. I.e., mechanical, pneumatic, or electronic level control of flash tank.
Cons:
- More potential leak points.
- More components increase chance of failure/down time.
- Electronic or Pneumatic level control keep system may be less reliable than mechanical level control.
- Though it is relatively minor consumption, these require electricity to run and therefore less efficient in recovering heat than a completely mechanical unit.
- Uses more floor space in boiler room.
“High-Capacity” Heat Recovery System
The next two designs are Madden Engineered Product designs as to the best of our knowledge no other OEM’s offer a significant design alternative to the above.

Our HC model boiler blowdown heat recovery systems are often used in larger industrial applications which utilize multiple boilers operating at high pressures and high capacities, generally watertube-type boilers. This heat recovery system design allows us to build units with boiler blowdown capacities up to 60,000 PPH.
In general, heat reclaim units are sized to provide about 10% maximum blowdown capacity from the boiler. So this design would be an appropriate blowdown system for a boiler room generating up to 600,000 PPH of steam. It could be used for boiler rooms with even larger steam production capacities in certain applications where the water quality is high and/or other reasons the surface blowdown requirements are lower than 10%. In general, an average amount of surface water blowdown from the boiler(s) is about 3% of steam production.
Pros:
- Has large overall boiler surface waste water blowdown capacities.
- Uses efficient, high-capacity u-tube bundle heat exchanger.
- Standard design is 100% mechanical, no part of the system uses electricity.
- Alternative level control equipment can be easily substituted.
Cons:
- Takes up more boiler room floor space.
- Heat exchanger is internal to the flash vessel, though easily removed.
- Standard level control is internal to the flash vessel.
“Most Compact” Heat Recovery System

The Madden “HV Model” heat reclaim design offers the most compact heat recovery system available on the market. The system as a whole is designed vertically and only takes up 2 sq. ft. in the boiler room.
This is accomplished by using a vertical shell and coil type heat exchanger integrally installed under the flash tank. The base design utilizes all internal components to further add to the compact nature of these systems.
Though maintenance may not be as easy to perform on these units, relatively speaking, the vertical coil design and simple mechanical float and drain assembly increases the service life of these units to a point we would not deem maintenance as a concern. Most HV model heat recovery systems last more than 10 years before anything wears to the point of a repair need. Vertical SS coils with cooling water on the shell side do not build scale. They are also 100% self-flushing as gravity will continue to drain the condensate even if not under pressure. These types of coils offer very long service life due to the fact that they have no sharp bends.
Pros:
- Most compact design available.
- Most easily installed ‘aftermarket’ system. If your existing boiler room does not utilize heat reclaim of the boiler waste water, this system is the easiest to implement in an existing boiler room’s footprint.
- 100% mechanically operated.
- Gravity draining design provides excellent service life and little to no relative down time.
Cons:
- All standard components are internal.
- Limited overall capacity (15,000 PPH of continuous surface water blowdown).

Quick Madden Heat Recovery System Pitch
At Madden Engineered Products we take pride in being an industry leader for boiler blowdown heat recovery system design help and product offerings. All of our designs can be customized to include external level controls among other design features and connection placements. We can provide performance and savings calculations to show what a heat reclaim unit would do in your boiler room. And specifically provide a return on investment report.

And above all, we strive to be the most consistent and responsive group to work with in regards to overall customer service.
Conclusion
For any boiler room energy and water conservation need, Madden has you covered. When dealing specifically with boiler surface water blowdown and bottom blowdown (see other articles on intermittent bottom blowdown here) we are an industry leader with over 65 years of experience.
We would welcome any inquiry dealing with initial system specification and design help to procurement and fabrication of a heat recovery system. If you have a question, equipment need, or anything in between please do not hesitate to reach out.
Thank you for reading our article, and have a great day!