What are B.T.U’s and why are they important in boiler blowdown processes and cost savings?
March 17, 2017 by Aaron Rhoade
B.T.U stands for British thermal unit and is commonly defined as the amount of heat required to raise the temperature of one pound of water by one degree Fahrenheit. Other than safety measures, BTU’s are arguably the most important factor to spend time and energy on when it comes to your boiler process. In the boiler room, B.T.U’s are their own form of currency. It takes a lot of energy to produce heat to boil water and to keep it boiling. The more efficient the boiler operator can be, the less energy, heat, and fuel are needed to produce steam.
Most boiler applications run 24/7/365. The energy to produce heat can come from natural gas, electric, or coal, among other sources and processes. So the smallest amount of B.T.U’s you can save will add up to big savings to your fiscal year’s bottom line.
There are many processes in the boiler room dedicated to maintaining and reusing already generated B.T.U’s. Condensate return pumps return condensed steam back to the boiler water as make up water, deaerator (D/A) tanks can reuse steam, and boiler chemicals are dosed into the boiler to make sure the water remains free of scale build up and of dissolved solids which hinder heat transfer from the boiler’s fire tubes to the water.
And last but not least, when your boiler(s) application calls for continuous blowdown to maintain clean water, one can recover B.T.U’s from this as well. Madden Manufacturing is one of the industry leaders in designing boiler blowdown equipment, and specifically blowdown heat recovery systems.
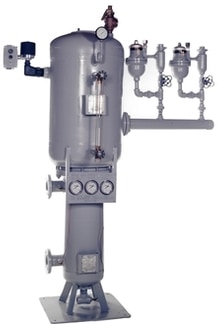
Concept of B.T.U’s & Heat Recovery
To get you in the right frame of mind for this topic, think about when you’re preparing to cook noodles and need to boil a pot of water. Some may simply fill a pot of water and turn the stove on high and not think twice about it. However, others may think to specifically fill their pot with the hottest water possible from the sink. In this case the water would come to a boil faster and the stove will not have to work as hard.
This is because the hot water from the sink contained more B.T.U’s than it would have otherwise. The stove didn’t need to produce as many B.T.U’s to reach boiling. Usually ground water or city water is around 60-70 degrees Fahrenheit, and your water heater can provide water closer to 100-110 degrees Fahrenheit. That is 40 less B.T.U’s needed to be generated by the stove top to reach boiling.
If you were not familiar with British Thermal units before, hopefully the concept where it concerns boilers is a little clearer now. So let’s see how the Madden Manufacturing Blowdown Heat Recovery System product line works.
Understanding boiler blowdown
Terms to know:
- Intermittent bottom boiler blowdown: this is when the boiler room operator occasionally blows down the dirty water at the bottom of the boiler. It is usually done by opening a valve for 30-60 seconds and then closing it. Commonly done at the beginning and end of each day.
- Continuous surface boiler blowdown: this is when the boiler is set up to constantly blowdown a small amount of the dirty water that forms at the top level of the boiler’s water line.
To keep suspended solids from building up and hindering steam production efficiency, some boilers need to constantly blowdown water which will then be replaced by clean make up water. The continuous surface blowdown is commonly 3-5% of steam production. (Need an industrial blowdown control valve for exactly that? Check out our Orifice Meter design).
First and foremost, back to safety, the boiler operator needs to get the temperature of the boiler blowdown water at or under 140 degrees Fahrenheit. This is a common benchmark to reach as 140 degrees or less will not cause severe burns should the blowdown make contact with skin. Blowdown tanks and blowdown separators are two of the more common products for handling intermittent, bottom blowdown, and are sometimes used for continuous surface blowdown as well.
If your boilers are doing any continuous surface blowdown, contact our factory for a savings calculation. There may be thousands of dollars to be saved from recovered B.T.U.’s in the blowdown, that you cannot get back using tanks and separators.
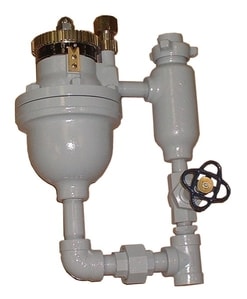
continuous blowdown flow control
And here’s why:
The first stage in handling intermittent bottom blowdown and/or continuous surface blowdown is dealing with the flash steam that is created when hot, high pressure boiler blowdown enters a low pressure vessel. With blowdown tanks and separators, this steam is safely vented to atmosphere.
The second stage is then to handle the remaining hot water. For boiler blowoff tanks, they are sized to hold one blowdown and cool it by natural convection, until the next blowdown comes and is quenched with the already cooled water. The water level will then rise over the overflow drain and safely go to the city sewer. With a blowdown separator, the remaining hot water after the flash steam has been vented gets immediately quenched and cooled with cooling water via a temperature regulating valve that allows cool city water to mix with the blowdown.
Not a big deal, remember, this is usually only happening for 30 seconds, twice a day. But if the boiler operator is utilizing continuous surface blowdown to keep the boiler water clean, this is happening all day long, every day.
So, to recap, with these devices HOT flash steam is vented to atmosphere, and remaining HOT blowdown water is quenched and drained to the city sewer.
In other words, B.T.U’s are allowed to float out of the building and into the sky and also directly drained to the city sewer.
Madden Manufacturing’s heat recovery systems can recover up to 90% of these otherwise lost B.T.U’s.
Operation of Continuous, Surface Boiler Blowdown Heat Recovery
With the concepts already laid out, explaining how a Madden boiler blowdown heat recovery system works is pretty easy.
When the hot continuous surface blowdown enters its flash tank, the flash steam that is produced when entering the low pressure vessel, is designed to be piped back to a D/A tank, instead of going to atmosphere. There are many valuable B.T.U’s in the flash steam that can be reused in the D/A tank so that less fuel/heat are needed to keep the water boiling in the boiler.
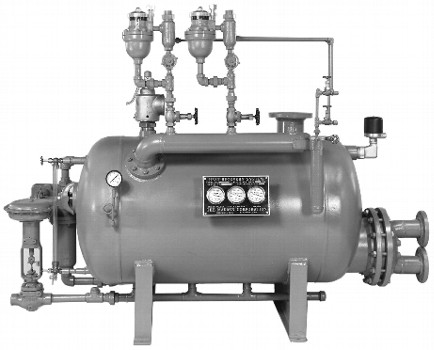
After the flash steam has been released and vented to the D/A tank, the remaining hot boiler blowdown leaves the bottom of the vessel when a float valve is activated and passes through/over either a coiled heat exchanger or U-tube type heat exchanger.
Here, the water the boiler operator uses as make up water, should first be piped through the heat exchanger of the Madden heat recovery system. It serves a dual purpose. First, this make up water (normally around 60 degrees) will be cooling the dirty boiler blowdown to under 140 degrees so that it can safely and legally drain to the city sewer. Second, on the flip side, it is picking up B.T.U’s from the hot boiler blowdown. It picks up heat.
So now instead of sending 60 degree make up water to the boiler, the boiler operator can constantly be sending make up water that has picked up 10+ degrees from the hot blowdown water. Much less fuel is then needed to continue boiling, and this starts to add up when you consider it is happening 24/7/365 days out of the year!
Conclusion
If your boiler room has a boiler or boilers utilizing continuous surface blowdown, and you do not already have some form of heat recovery, give us a call! We would love to start working on this project with you to save B.T.U’s and therefore thousands of dollars.
Email: info@maddenep.com
Ph: 800-369-6233